Cemented carbide features
Cemented carbide is known as the “teeth of industry”. Its application range is very wide, including engineering, machinery, automobiles, ships, optoelectronics, military industry and other fields. The consumption of tungsten in the cemented carbide industry exceeds half of the total consumption of tungsten. We will introduce it from the aspects of its definition, characteristics, classification and use.
First, let’s take a look at the definition of cemented carbide. Cemented carbide is an alloy material made of hard compounds of refractory metals and bonding metals through powder metallurgy. The main material is tungsten carbide powder, and the binder includes metals such as cobalt, nickel, and molybdenum.
Secondly, let’s take a look at the characteristics of cemented carbide. Cemented carbide has high hardness, wear resistance, strength and toughness.
Its hardness is very high, reaching 86~93HRA, which is equivalent to 69~81HRC. Under the condition that other conditions remain unchanged, if the tungsten carbide content is higher and the grains are finer, the hardness of the alloy will be greater.
At the same time, it has good wear resistance. The tool life of cemented carbide is very high, 5 to 80 times higher than that of high-speed steel cutting; the tool life of cemented carbide is also very high, 20 to 150 times higher than that of steel tools.
Cemented carbide has excellent heat resistance. The hardness can remain basically unchanged at 500°C, and even at 1000°C, the hardness is still very high.
It has excellent toughness. The toughness of cemented carbide is determined by the bonding metal. If the bonding phase content is higher, the bending strength is greater.
It has strong corrosion resistance. Under normal circumstances, cemented carbide does not react with hydrochloric acid and sulfuric acid and has strong corrosion resistance. This is also the reason why it can be unaffected by corrosion in many harsh environments.
In addition, cemented carbide is very brittle. This is one of its disadvantages. Because of its high brittleness, it is not easy to process, it is difficult to make tools with complex shapes, and it cannot be cut.
Third, we will further understand cemented carbide from the classification. According to the different binders, cemented carbide can be divided into the following three categories:
The first category is tungsten-cobalt alloy: its main components are tungsten carbide and cobalt, which can be used to produce cutting tools, molds and mining products.
The second category is tungsten-titanium-cobalt alloy: its main components are tungsten carbide, titanium carbide and cobalt.
The third category is tungsten-titanium-tantalum (niobium) alloy: its main components are tungsten carbide, titanium carbide, tantalum carbide (or niobium carbide) and cobalt.
At the same time, according to the different shapes, we can also divide the cemented carbide base into three types: spherical, rod-shaped and plate-shaped. If it is a non-standard product, its shape is unique and needs to be customized. Xidi Technology Co., Ltd. provides professional brand selection reference and provides customized services for special-shaped non-standard cemented carbide products.
Finally, let’s take a look at the uses of cemented carbide. Cemented carbide can be used to make rock drilling tools, mining tools, drilling tools, measuring tools, wear-resistant parts, metal molds, cylinder liners, precision bearings, nozzles, etc. Sidi’s carbide products mainly include nozzles, valve seats and sleeves, logging parts, valve trims, sealing rings, molds, teeth, rollers, rollers, etc.
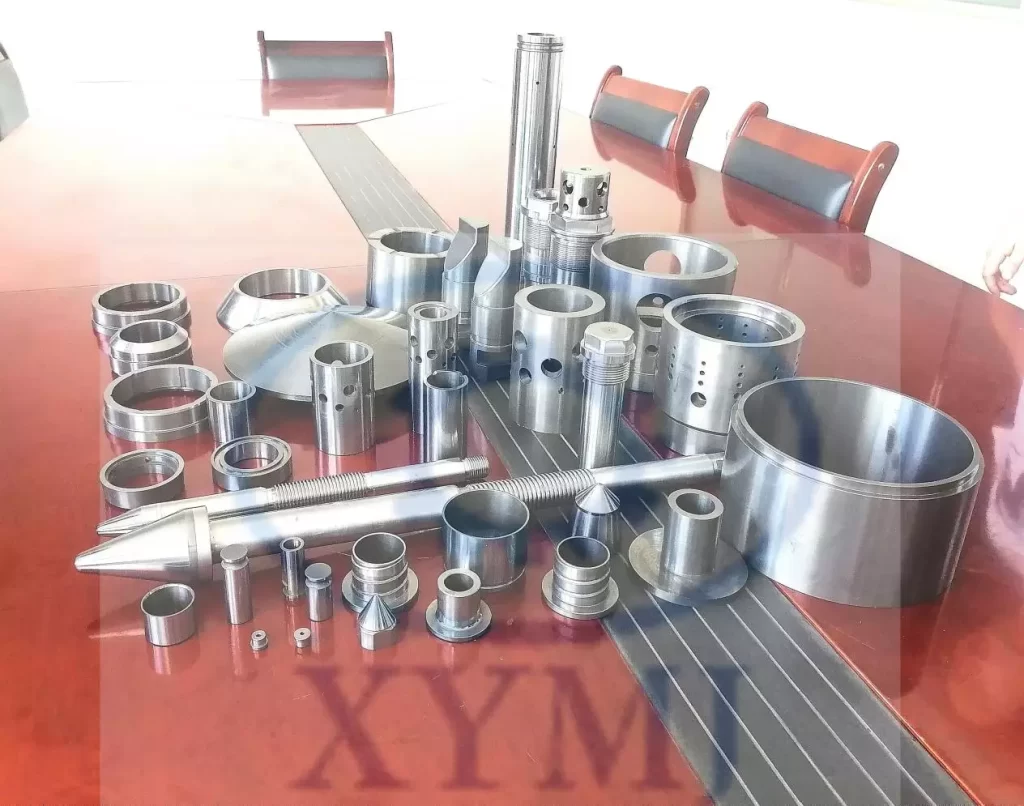